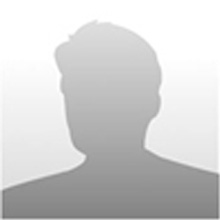
Quality In Charge in ESTC
Job Experience
Quality In Charge
ESTC
October 2016 to December 2016
? Contribute to the identification of opportunities for continuous improvement to Quality planning systems, processes and practices taking into account ?international best practice?, improvement of business processes, cost reduction and productivity improvement.
? Review, analyze and recommend methods and procedures to develop and utilize the most economically advantageous and efficient means of delivering the Quality products.
? Prepare statements and reports timely and accurately to meet company and department requirements, policies and standards.
? Analyze product quality index, package quality index and micro results trend
? Translate the Quality strategy into plans in order to execute it while ensuring alignment with the optimum product Quality.
? Supervise the major quality issues in order to ensure necessary alignment to the master programs and minimize related issues.
? Supervise Quality program updates and related controls to ensure activities remain abreast with the respective programs and plans.
? Supervise completeness of work and report in order to comply with Management expected standards of Quality project timelines and specifications.
? Identify and facilitate cost improvement opportunities throughout the business as required.
? Assemble cost control and statistical data, as needed, in order to support Operational excellence.
? Guide all assignments through a systematic development process thereby ensuring product quality, appropriate project prioritization and resource allocation.
? Undertake the necessary optimization of Quality lab inventory ? in conjunction with QC Team.
? Ensure effective coordination of the value chain activities in order to ensure Quality efficiency.
? Control the utilization, handling and storage of analysis, Trend data and cost control records and keep a copy of national/ international quality standards and other referential specifications to maintain the necessary documentation in-case of future requirements. Maintain relevant procedures
Quality assurance Supervisor
Awal Da
June 2012 to January 2016
Manage the laboratory functions, and ensure effective, timely and efficient performances and analysis to maintaining company specifications and cost objectives.
? The duties and responsibilities included routine activities concerned with the physico-chemical and microbiological testing of mixes and finished products, both fresh and long life, and the necessary documentation associated with it; checking the raw materials and supplies to make sure the quality standards have been met; and a unique job of developing new product.
? Ensure an appropriate laboratory test/testing equipment procedure is introduced to maintain effective Q.A. With in the production. Provide technical information, advice or assistance to Management on Quality issues or other areas that may affect quality in any way.
? Control the Aseptic packaging lines and gives technical advise to the Tetrapak operators.
? Monitoring the Aseptic processing and ensuring the Aseptic packaging integrity.
? Developing and maintaining the product release procedures and monitoring product shelf life Study.
? Playing a key role in systematic troubleshooting and corrective action planning.
? Agree specifications on raw and packaging material and recommending purchase department to maintaining and improving standards.
? Co-ordinate the development and implementation of Food Safety Management Systems in conjunction with Management & Staffs.
? Developing and updating quality system through analysis, auditing and administration.
? Initiate HACCP programme for new lines/ Products and review existing HACCP, Conduct Quality and Hygiene awareness training for staffs.
? Work closely with concerned departments to assess process capability and improvement, advice and assist quality related matters. Implement product improvements and product developments.
? Liase with legislative and standards enforcement bodies such as Bahrain Standards /SASO to ensure that relevant directives are complied with. Halt Production, quarantine, reject or recall non ? complying product or product suspected of non-compliance at any time.
? Work closely with Sales & Production Manager to investigate and resolve quality issues arising through customer complaints or internal problems and give technical instructions to the Management.
? Develop, maintain and improve customer complaint analysing process.
? Monitor hygiene and housekeeping standards, conducting in house inspections and recording and analysing related data.
? Monitoring waste handling and pest control services to ensure that factory remain waste and pest free.
Quality Executive
Elite Naturals Private Limited, Hosur, Tamil Nadu, India
April 2011 to June 2012
Over all supervision on laboratory functions, and ensure effective, timely and efficient performances and analysis to maintaining company specifications and cost objectives.
? Monthly action planning for quality improvements
? Preparation of Monthly quality review Report
? Ensuring the quality of products for export shipment by segregation and loading inspection.
? Product release inspection-Microbiological, chemical and physical analysis of finished goods.
? Customer complaint closing
? Playing a key role in systematic trouble shooting and corrective actions
? Ensure an appropriate laboratory test/testing equipment/procedure is introduced to maintain effective Q.A. With in the production. Provide technical information, advice or assistance to Management on Quality issues or other areas that may affect quality in any way.
? Co-ordinate the development and implementation of Food Safety Management Systems in conjunction with Management & Staffs?
? Maintain and update quality system through analysis, auditing and administration.
? Initiate HACCP program for new Products and review existing HACCP, Conduct Quality and Hygiene awareness training for staffs.
? Initiate, manage and follow up investigation /audits of all quality issues and problems. Ensure Corrective action/modification is implemented and measures are incorporated into quality system to prevent recurrence.
? Work closely with concerned departments to assess process capability and improvement, advice and assist quality related matters.
? Work closely with Sales & Production Manager to investigate and resolve quality issues arising through customer complaints or internal problems and recommend Management any procedures or method that need to the introduced or corrected.
? Monitor hygiene and housekeeping standards, conducting in house inspections and recording and analyzing related data.
? Monitoring waste handling and pest control services to ensure that factory remain waste and pest free.
Quality Controller
Foster Hot breads
May 2008 to November 2008
Online Quality control
Manage the laboratory functions, and ensure effective, timely and efficient performances analysis to maintaining company specifications and cost objectives.
? Monitor hygiene and housekeeping standards, conducting in house inspections and recording and analysing related data.
? Monitoring waste handling and pest control services to ensure that factory remain waste and pest free,
Education
Msc in Food Technology
University of CalicutCurrently studying
Bsc food Technology
University of CalicutCurrently studying
Languages
IT skills
Other Skills
More Baiju
Career Goals
Industries of interest
Areas of interest
Availability to travel and work outside the city
No