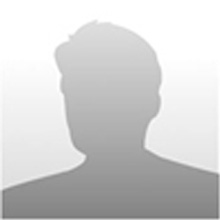
UPD WC Regional Buyer in UPD distribution
Job Experience
UPD WC Regional Buyer
UPD distribution
October 2015 to Actually working here
?Procurement and replenishment of stock through implementing working capital optimization when purchasing?Ensure the accurate maintenance of the buyer portfolio ensuring all captured field details are current and correct by Procurement Admin.?Monitor and track performance indicators of the buyer portfolio to ensure certain Supply Company targets and incentives are achieved?Ensure that all products procured and sold are within the legal requirements relevant to the Pharmaceutical Industry
Senior Buyer
Alpha Pharm Pharmaceutical Wholesalers
February 2014 to September 2015
Monitor and track performance indicators of the buyer portfolio to ensure Ensure that all products procured sold are within legal requirements Co-ordinate regularly meetings with Supplier companies within the buyer portfolio to facilitate healthy relationship, place orders and manage and resolve any issues
Monitor financial implications of procurement portfolioCustomer Service and Marketing PrinciplesWarehouse OperationsSupplier Negotiations
Raw Material Buyer
Vital Health Foods
February 2013 to December 2013
Purchasing, Planning, Forecasting, Imports Controller, Finance Planning, Sourcing. Review and carry out remedial actions on MRP/MPS exception messages daily for production and materials ?Establish and maintain effective working relationships with all areas in the different departments and supporting functions ?Respond to changing customer and production requirements via the daily management of SOLS and weekly board meetings ?Escalation of significant production issues to Planning Manager and stakeholders. ?Control stock of intermediates and raw materials to ensure that write-off are minimised, and supplier defined lead-times and MOQs are adhered to. Work to agreed stock policies and regulatory requirements ?Works closely with the Planners to support the Rough Cut Capacity Process and ensure that it delivers an achievable plan in the 3 month time period. ?Play a key role in ensuring the success of the SCP process for the various Value Streams ?Team member of cross-functional projects, with regard to supply chain processes and continuous improvement for in the various Value streams ?Maintain and improve the Supply chain and all associated processes (eg. KPI, CSA, SCP, SCIM, S&OP) and supply chain systems (eg. Syspro, etc).
Materials Resource Planner for LVS, TVS & AVS
GlaxoSmithKline
October 2010 to January 2013
?Review and carry out remedial actions on MRP/MPS exception messages daily for production and materials ?Establish and maintain effective working relationships with all areas in the different Value Streams and supporting functions ?Respond to changing customer and production requirements via the daily management of SOLS and daily board meetings ?Escalation of significant production issues to Supply Plan Managers and Value streams. ?Control stock of intermediates, raw materials and print materials to ensure that write-off are minimised, and supplier defined lead-times and MOQs are adhered to. Work to agreed stock policies and regulatory requirements ?Works closely with the Supply Plan Managers to support the Rough Cut Capacity Process and ensure that it delivers an achievable plan in the 3 month time period. ?Play a key role in ensuring the success of the SCP process for the various Value Streams ?Team member of cross-functional projects, with regard to supply chain processes and continuous improvement for in the various Value streams ?Maintain and improve the Supply chain and all associated processes (eg. KPI, CSA, SCP, SCIM, S&OP) and supply chain systems (eg. Manugistics, SOLS, JDE, BPCS etc).
Senior Packaging Estimator/Materials Planner
Nampak Cartons & Labels
April 2004 to September 2010
?Processing estimates, Prepare and type quotations, ?Ensuring requirements on reps/customer?s enquiry are adequately defined, the plant have the capability to manufacture the product to customer?s specifications, ?Prepare lay-outs ? taking into account material availability, plant capacity, standard sheet sizes and delivery date, ?Liaison with internal customers w.r.t. availability of raw material, prices, specs and production lead times, Check estimates for accuracy, ?Maintain Estimating efficiency report, Allocation of raw material to work tickets and/or find alternative/substitute raw material and re-scheme if necessary, ?Liaison with Production planner on raw material availability prior to firming up the following 2 week?s production plan, ?Raw Material Purchasing, Follow up & expediting of main raw materials from suppliers, ?Loading of orders & resolving queries and outwork requirements and pricing, ?JD Edwards Estimating system, ERP System & queries, Technical support to team, ?Raw Material Forecasting (quarterly & yearly) using Demand Planning, utilize A.P.S.(Advance Planning Schedule), ?Assist in reducing working capital on raw materials, ?Conduct periodic stock counts, Manage aged stock in WIP (work in progress), ?Generate purchase requisitions of raw materials, Reconcile and replenish finished goods consignment stock, ?Attend work order close out process and meetings, Keeping adequate stock levels, ?Requester/Processor on Commerzone, Vortalbuy & J.D. Edwards, ?Utilizing B.I. reports (Business Intelligence) for material forecasting & requirements, Production & Administrative queries, ?Submit weekly Astride production material requirements + ensure raw material is available when required by production, Manage inventory ageing, ?General/Technical support to estimating colleagues, ?Liaise daily with production planner and logistics manager/commercial manager.
Printing Estimator
Colourtone Press/ Aries Packaging
June 2000 to March 2004
At this small commercial company I had my hands in everything. Doing quotes, worksorders, processing of customer orders, supply costing, customer service, planning, procurement and admin. Thrived on new challenges which I conquered. Good time management. ?Prepare quotations, Processing estimates, ?Ensuring requirements on reps/customer?s enquiry are adequately defined and the plant have the capability to manufacture the product to customer?s specifications, ?Prepare lay-outs ? taking into account material availability, plant capacity, standard sheet sizes and delivery date, ?Liaison with purchasing officer regarding availability of raw material, price, specs and lead times, ?Processing Works Orders, ?Check estimates for accuracy, ?Allocation of raw material to work tickets and/or find alternative raw material and re-scheme if necessary, ?Liaison with Production planner on raw material availability prior to firming up the following week?s production plan, ?Actively involved in cost saving projects, ?Raw Material Purchasing ?Client Liaison, Data Capturing, Production Planning
Printing Estimator
ToneGraphics
November 1996 to May 2000
?Prepare quotations, Processing estimates, ?Ensuring requirements on reps/customer?s enquiry are adequately defined and the plant have the capability to manufacture the product to customer?s specifications, ?Prepare lay-outs ? taking into account material availability, plant capacity, standard sheet sizes and delivery date, ?Liaison with purchasing officer regarding availability of raw material, price, specs and lead times, ?Processing Works Orders, ?Check estimates for accuracy, ?Allocation of raw material to work tickets and/or find alternative raw material and re-scheme if necessary, ?Liaison with Production planner on raw material availability prior to firming up the following week?s production plan, ?Actively involved in cost saving projects, ?Raw Material Purchasing ?Client Liaison, Data Capturing, Production Planning
Education
CPIM (Certified in Production & Inventory Management
SAPICS (Afganistán)January 2012 to December 2015
PPIM
SAPICS (Sudáfrica)June 2010 to October 2010
ND DIPLOMA PRINT MANAGEMENT
CPUT (Sudáfrica)February 2008 to November 2011
Matric
Princeton Secondary School (Sudáfrica)January 1998 to December 1992
Languages
English
Advanced
IT skills
Word, Excel, Access, Internet, E-mail, JD Edwards, Winprint, BPCS, Syspro, Powerpoint,
Advanced
Other Skills
More Marvin Anthony
Career Goals
To be an effective asset to any organization to achieve their goals.
Industries of interest
Areas of interest
Availability to travel and work outside the city
Yes