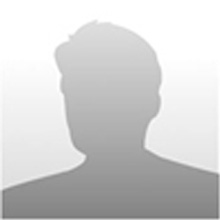
Latinamerica Operations Manager in General Mills
Job Experience
Latinamerica Operations Manager
General Mills
February 2012 to Actually working here
Optimize external manufacturers cost, quality and productivity for GMI product plataforms. Develop finish product category strategies. Recommend and implement proces solutions to ensure continuos improvement of results for GMI products.
Operations and Manufacturing Consultant (Acting Plant Manager)
PILSAC S.A. de C.V.
September 2010 to November 2011
Work as consultant creating operations strategies and working on manufacturing processes optimization and planning. Implementing Lean Manufacturing at PILSAC S.A. de C.V. and other continuous improvement strategies aimed to increase productivity, build teamwork and cultural change in the plant while maintaining a high morale and enthusiasm.
Manufacturing Manager, Sr
Wm Wrigley Jr. Mexico
March 2006 to May 2010
Responsible for total plant operation, manufacturing cost strategy, budgets, as well as production and maintenance planning, maximizing the use of assets, as well as material and human resources. During my tenure at Wrigley successfully implemented and achieved: ? Implemented key performance indicators in the areas of production, maintenance, safety and finance. ? Implemented Management by Objectives at all levels in the plant. ? Implemented Lean Manufacturing and TPM(7 Pillars, Stage 5); which helped increase productivity to levels up to 82.5% in OEE. Using the Japanese Institute of Productive Maintenance (JIPM) methodology. ? Reduced usage variances in 90%, diminished work in process materials and complaints at the lowest regional level; and reduced production cost in 18% while increasing participation on safety initiatives reducing the risk degree before governmental agency. ? Achieved Food Safety Certification before international agencies (BRC, IFS). ? Successfully implemented HACCP in plant. ? Implemented Lean Manufacturing tools, Kaizen y Total Productivity Management (TPM). ? Achieved quality certification by WQMS (ISO) for the plant. ? Implemented Kaizen events which lead to increase productivity and reduce wastes in varios areas of the plant. ? All the above mentioned achievements while maintaining a high sense of workteam, quality, productivty and responsibility from personnel, as well as a results oriented attitude.
Commercial Manager, Technology and Innovation
Solder Mexico
February 2006 to December 2006
Adhesives Formulation Company Focused to Footwear Manufacturing Sector. Private bussiness with minor ownership participation for the new markets sector developed, other than leather and footwear. Responsible for commercialization and technical support for adhesives sales. In charge of creating the production infrastructure for these products, for which increased sales in 60%.
Freelance Consultant
INDEPENDENT CONSULTANT
May 2004 to January 2005
? Contributed to the implementation of Six Sigma projects and Quality Systems for Laboratorios Kendrick S.A. ? Participated in defining new products, Project Management, Quality and Lean Manufacturing systems at the Berol Mexico S.A. de C.V. manufacturing plant ? Implemented Testing Laboratory at Desmex S.A. de C.V.
Production Manager
Rohm and Haas
March 2001 to March 2004
Responsible for production strategy, budget and planning, warehouses, engineering and research, as well as development of the different site plants (Polyacrilates, Ion Exchange, Acrylic Emulsions, and Biocides). Led the cultural change in site, which helped to exceed expectations in the areas of safety, quality, cost reduction and productivity. Negotiating with the union in order to achieve the goals set. Achieved production records and developed self managed teams philosophy. Implemented six sigma and world class manufacturing techniques that led to reduction of conversion costs, decreased off grade inventory in 70%; waste reduction with savings of 26%; diminished inventory level in US$800K; lessened variations in US$400K. Increased participation of personnel in 80% on safety initiatives; and augmented plant capacity in 12% without capital investment. All this with a budget of US$7.5MM for 2 polymer production plants and two formulation plants. Managing a team of 105 employees; including production planning functions. Managed all the transition and negotiations to shut down one of the plants under my supervision while maintaining the moral and enthusiasm of the team. ? Implemented initiatives to improve performance in EH&S metrics encouraging involvement of all personnel. ? Implemented performance indexing and manufacturing techniques that were deployed at regional level in Latin America. ? Implementation and training on SAP at Latin America level for manufacturing, quality, order to cash and maintenance.
Manufacturing and Technology Center (MTC)Manager
General Electric International
October 1999 to February 2001
Personnel and resources coordination activities management required for development of the different projects committed to with the company?s subsidiaries. Directly responsible for the following projects: ? Led team to improve powder coating process and reduce out of specs product in 10%, using Six Sigma tools. GE-Mabe. ? Developed suppliers for key raw materials using Design for Six Sigma Tools. GE-Prolec. ? Led team to increase productivity ($750K) and capacity (10%) of a polymerization plant, using Six Sigma tools. GE Plastics Division ? Led team and project to improve refrigerators? liner plastic material for Mabe-GE Appliances increasing customer satisfaction by 12%, through Six Sigma tools. GE Appliances ? Helped customer of GE Plastics to improve performance of engineering plastics and epoxy resins, using Six Sigma. GE Plastics Division.
Plant Engineering Leader
BASF Mexicana
September 1997 to October 1999
Led the start up of the primary and secondary extrusion lines; and participated along with the leadership team in the start up of the polymerization plant for an engineering plastics resin. Participated in the planning strategy for the construction of an agrochemical plant as well as the selection, training and development of a team of 14 engineers to operate such a plant. ? Designed and implemented EH&S standards. Managed budget, maintenance and engineering activities for an engineering plastics resin plant (ABS), supervising 10 employees. ? Worked along with the engineering team in the development of the basic engineering, final construction stage, commissioning and start-up of an ABS plant in Altamira Mexico. ? Participated in the planning strategy to shutdown and start-up a plant for ABS resin, after 2 years of continuos production, for maintenance activities, in Gemany. ? Successfully start up the primary extrusion and compounding section of the ABS plant in Altamira. ? Participated in the basic engineering stage and HAZOP analysis of the BAS635H? project (new herbicides plant). ? Participated with the manufacturing team in the start up of a new herbicides plant in Germany.
Process Engineer
Dow Quimica Mexicana
October 1992 to December 1994
Led project to upgrade a herbicides and an insecticides plant; responsible for the maintenance of these plants and actively participated on the strategic planning for the bioremediation of the site. ? Led program for waste reduction in plant generating benefits for US$200K. ? Designed and led projects to optimize filling lines, generating benefits for US$120K. ? Managed budget and maintenance program for plants improving performance in 10%. ? Coordinated, controlled and planned investments for the plants with a capital budget of US$3.5MM. ? Participated in the design of the emergency plan for the DOW manufacture in Mexico. ? Successfully coordinated the areas of Engineering, Safety and Loss Prevention before the corporate consolidated audit, obtaining outstanding results. ? Designed herbicides and insecticides plants upgrading project, resulting in an investment of US$6MM
Education
Master of Business Administration (MBA)
[Otra]Tecnologico de Monterrey (ITESM) (México)January 2009 to January 2012
M.A.
[Otra]Universidad Iberoamericana, Ciudad de México (México)January 2002 to January 2004
Ph.D.
[Otra]University of Arizona (México)January 1994 to January 1997
M.Sc.
[Otra]University of Arizona (México)January 1990 to January 1992
Ingeniero Quimico
Universidad de Guanajuato (México)January 1984 to January 1989
Languages
IT skills
Other Skills
More Pablo Adan
Career Goals
BUSINESS STRATEGIST IN MANUFACTURING PROCESSES, WITH AMPLE EXPERIENCE IN CONTINUOUS IMPROVEMENT PROCESSES THROUGH LEAN MANUFACTURING, SIX SIGMA, AND TPM METHODOLOGIES EXECUTIVE SUMMARY Nineteen years national and international experience in important multinational leading manufacturing companies. Broad business perspective applied to manufacturing environments using Six Sigma, Total Productive Maintenance (TPM), and Lean Manufacturing methodologies for an efficient operations and quality control, as well as cost reduction with great financial impact. Organized, methodical, with strategic vision, and oriented toward results; motivating leader, positive change generator. Ease to develop and motivate successful work teams. Good communication skills, as well as sensitivity to identify, analyze, and solve problems. KEY ACHIEVEMENTS Designed and implemented productivity strategies and performance indexes that led the Wrigley Mexico manufacturing plant to the second best performance in North America Region in 2 years. Participated in the development of the strategy, design, and establishing of the GE Manufacturing and Technology Center in Mexico, to provide technological service to the company?s subsidiaries in Mexico, generating savings of approximately $12M USD. Coordinated, controlled, and participated in investment planning for the modernization of the herbicides and insecticides plants for a total amount of $3.5MM USD at Dow Michigan, in a record time for the company. Collaborated in basic engineering, constituting the work team, construction and start up of the herbicide and copolymers plant, both projects with an estimated value of $170M USD at BASF. Achieved savings for $1.6MUSD through different projects using Lean Manufacturing and TPM in 1 year in Wrigley. Increasing productivity to levels of 82% in OEE. Implemented Lean Manufacturing Tools and Behavior Based Safety, creating a continuous improvement culture at Rohm and Haas.
Industries of interest
Areas of interest
Availability to travel and work outside the city
No
Interests and hobbies
Managemente Training, Chemical Technology, Improvement and Productivity Strategies