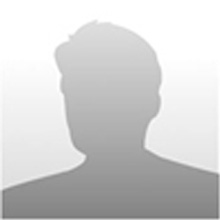
Supply Quality Development in Gibela (Alstom Transport)
Job Experience
Supply Quality Development
Gibela (Alstom Transport)
October 2013 to Actually working here
The primary purpose of this position is to ensure that the product or service an organisation provides is fit for purpose, is consistent and meets both external and internal requirements. The key responsibilities of the position are as follows, but not limited to: ? Supplier Quality Performances: - Set Suppliers Quality Commitments in accordance with Alstom Transport Sourcing Quality objectives - Support Supplier Product Quality Development / Supplier Quality Assurance Managers - Lead regular Quality reviews with the key suppliers ? Suppliers? development: - Lead supplier development plan: - Drives actions and improvement plans - Enforce problem solving method analysis - Support the key-suppliers in the changeover to ?Quality Assurance?: - Identify weak and strong points of the suppliers? quality organizations - Propose quality improvement levers - Report problem progress check ? Product Approval: - Define and document the supplier quality deliverables at every sourcing milestone from business award till First Article Inspection - Validate the product is conform to specifications and the supplier production capability to deliver conform parts - Prepare and pronounce status GO / NOGO for FAI and animate the action plans - Ensure with the suppliers that warranty issues are managed - Capitalize in project development through ROE in SQA and warranty results ? Ways of Working: - Set up quality standards & tools - Set up suppliers Return On Experience ? Audits: - Ensure that the relevant audits are performed & followed up on its commodities panel (Process audit, Co-Development audit, Quick supply chain assessment, Sustainable Development audit) - Ensure safe transfer processes ? Reporting, tools and network: - Provides regular reports to Sourcing community and respective stakeholders (including Key Process Indicators, warning systems) - Improve functional standards, processes, tools and methods towards operational excellence
Quality Projects and Development
Rheinmettal Denel Munition
January 2013 to September 2013
The main purpose of this position is to implement and maintain Quality Engineering Systems and Technical Support for the entire lifecycle with special reference to Process Development and Product Manufacturing Methods, Design and Research, Inputs, Development, Production and Testing as well as problem solving. Primary Task: - ? Implement, monitor and control a quality engineering system to ensure quality of manufacturing outputs. ? Implement, monitor and control supplier quality during process re-qualification / verification. ? Support Process Development and Business Solutions in qualification of new products and processes. ? Investigation of Internal Customer Complaints. ? Ensure continuous maintenance and control of all Tooling. ? Provide leadership and direction as well as Technical Guidance in the Quality Engineering Area. ? Formulate and implement a new strategic direction for the Quality Engineering Area. ? Provide the required procedures, to execute Quality Engineering Services in achievement of the RDM Business Plan ? Provide the required Special Procedures Work Instructions to execute quality services in attainment of the RDM Business Plan. ? Implementation of the strategic direction for Quality Engineering from Manager: Technical Support Services. ? Manage allocated resources to effectively deliver a quality service in the quality engineering area. ? Establish a plan for development and growth of Quality Engineering Personnel. ? Provide input to HR department for succession planning. ? Ensure retention of skills ? To develop, train and motivate staff to attain high levels of efficiency in their jobs so as to satisfy customer needs ? To control expenses within the approved budget ? To control expenses within the approved budget
Senior Supply Quality Engineer
Bell Equipment
January 2012 to December 2012
The purpose of this position is to audit suppliers, develop suppliers and implement corrective action at the supplier for both local and international. ? New Suppliers ? Where the sourcing team identify a potential supplier to supply Bell Equipment, I am responsible to audit the supplier and asses the supplier?s capability of meeting our quality management system requirements. ? Verify supplier quality management system effectiveness. ? Verify supplier capability to manufacturing good parts at cost effective process on time. ? Coordinate supplier process capability studies and ISIR samples submission. ? Current Supplier ? Coordination supply quality problem analysis and implementation of containment action. ? Coordinate supply root cause analysis, permanent corrective action implementation and verify the implementation and effectiveness of the corrective action. ? Ongoing supply audit to identify area for improvement. ? Supply Quality Problems ? Responsible to close off all supply quality problem reports (NCR) both for Bell Equipment ? Richards Bay and Bell Equipment Germany. ? Give feedback to management on the root cause and corrective action taken by supplier for all supply quality issues that resulted in production line description for both Bell Equipment Richards Bay and Bell Equipment Germany. ? Conduct investigation and implement corrective action on all warrant issue which are caused by supplier. ? Give feedback regarding the supplier performance (for year-end Supplier of the Year)
Senior Quality Engineer
Lumotech South Africa
April 2010 to December 2011
The purpose of this position is implement and adherence the Quality Management System, define and rectify problematic areas and assist departments with quality problem and develop and implement new problem solving techniques. Coordinate customer first sample submission, test requirement, capability studies and supplier approval product approvals. ? Full responsible for the following customer: VWGSA, Nissan, Ford and Street-Light (NMM) o Initial Approval Process o Quality Management Systems o Quality Problems o Continues Improvement o Quality Audits o Warrant Claims o Parts Per Million targets ? Ensure compliance with Quality and Engineering Systems ? Ensure control plan and inspection instructions are understandable and effective ? To be responsible for all aspects with regard to internal and external initial sample inspection requirements ? Conduct photometric tests for headlights and secondary lights ? Responsible for the planning, and evaluation of internal or external E.S. Testing ? Assist with supplier regarding PSW submissions ? Quality problem investigation and rectification ? Implements all necessary controls in manufacturing areas ? With Quality Compile documentation and graphs for all activities i.e. Scrap, Reworks, Monthly Reports Assist, assist with quality budgeting and costing ? To deputise for quality engineering manager when required ? Liaison and communicate with senior management including customer and suppliers ? Has the authority to intervene in any process which does not produce quality products as laid down by internal and external specification and procedures Decision Making: ? Decide if supplier is competent to conduct business with Lumotech ? Decide on timing for customer approval for I.S.I.R./ FSR/ PSW ? Stop the manufacturing process due to non-conformance products ? Decide on budget for quotations for new projects regarding quality ? Decide on non-conformance product fitness for use
Senior Supplier Auditor[
VWSA
February 2009 to March 2010
The purpose of this position is to conduct quality system and process audits of all local and export external suppliers (current and proposed) in order to determine the quality capability of VWSA?s supplier base. ? Evaluate the supplier quality management system and processes to determine their quality capability thus measuring the quality risk to Volkswagen should components be sourced ? Negotiate and support the supplier management team to convince the team on the need of improvement where resistance is encountered ? Produce detailed audit reports of supplier evaluation findings for distribution internally at Volkswagen and third parties ? Advice and assist proposed and existing supplier in planning of production and quality systems and processes for new developments ? Define and assist suppliers in the development of corrective action programmes resulting from inadequate production and quality systems ? Co-ordinate and monitor improvements to agree upon action programmes for new project developments with suppliers ? Assist, support and liaise with VWSA engineering and purchasing on supplier and component developments
Quality Engineer
VWSA
April 2008 to January 2009
The basic purpose of the position is to conduct a vehicle electrical audit, investigate problem highlighted by Final Vehicle Audit and Test Centre, coordinate implementation of short term and long term corrective action. ? To conduct product audit focusing on the electrical functions and verify that the product has been build according to specification ? Conduction problem investigation on all major electrical problems which are pick up by Final Vehicle Audit, Test Centre, production or external customer (Japan, Australia etc.) ? Coordinator the implementation of containment action, root cause analysis and permanent corrective action ? Updating data base for Top management on fault per vehicle status ? Present root cause analysis and corrective action to the WVSA top management.
Supplier Development Coordinator
General Motors
June 2006 to March 2008
? Carefully monitor the Procurement process through the Sourcing Table for new material & establish if the business will be placed with existing Suppliers or New Suppliers ? Establish the volume of material that will be required identifying forecast peaks ? Initiate a Supplier-capability survey to establish Suppliers capacity & capability including Machinery, Manpower & administrative ability to interpret our electronic releases & confirmations ? Identify constrains, if any ? Ensure correct call-in methodology is applied (i.e. KANBAN / SILS or Deliver to schedule) ? Visit Supplier to get first-hand view of Supplier capabilities & facilities ? In conjunction with SQ&D monitor the PPAP / Run@Rate testing ? in order to ensure initial Pilot build & subsequent production ramp-up, support capability ? Ensure MHE are aware of the new material & that correct packaging is applied by the Supplier for delivery as well as that suitable line side racking is available ? Ensure deliveries of Line Trial Material is delivered timorously & stored in the Line Trail store ? Ensure Production material is delivered well in advance ? Implementation of Lean Manufacturing methodology at the supplier to improve productivity and cost effectiveness. ? React by interfacing with poor performing Suppliers (based on alerts emanating from either MO&C, SQ&D or Procurement) ? Raise Problem Report & Resolution (PRR) documentation & forward to Supplier Management ? Visit Supplier to establish cause/effect & to review Management commitment, Facilities, bottle necks etc. ? with a view to immediately recovering & reverting to scheduled delivery schedules ? Development of a corrective action plan in conjunction with Senior Management & obtain Management buy-in ? Review the Action plan regularly & amend as required ? Conduct process audit to verify process stability & identify opportunity for improvement ? Appraise MO&C as well as SQ&D / Procurement of developments & highlight areas of potential risk
Supplier Quality Engineer
General Motors
February 2002 to May 2006
Continuous Improvement at suppliers: ? Identify suppliers with stable processes and consistently good quality performance ? Confirm they have a continuous improvement plan in operation (e.g. GP-8) ? Guide and assist when necessary to effect continuous quality improvements ? Provide feedback to supplier on customer experience Monitor Supplier Performance measures and improvement Plans: ? Monitor on-going supplier quality performance i.e. Major Disruptions, PRR?s and PPM ? Provide feedback to suppliers and division management ? Identify top problem suppliers and top problems with each ? Drive continuous improvement through focused corrective action plans at suppliers ? Ensure regular communication of goals, expectation and performance ? Provide input for sourcing decisions and Supplier of the Year selection Supplier Problem Reporting, Containment and Corrective Actions ? Review daily feedback from SPI, Audit Bay, Service, etc. ? Be appraised of all PRR?s raised especially Major Disruptions ? Liaise with Technical Support / Service for reworks to vehicles already shipped to dealers ? Ensure Management presentations on supplier related problems as required ? Develop and maintain processes to ensure DMC manufacturing site support. Controlled Shipping: (Containment) ? Initiate CS level 1 process for repetitive PRR?s, warranty problems or Major Disruption ? Ensure CS is set up per procedure and audited for compliance by facilitator ? Initiate CS level 2 if warranted, ensuring all containment costs are debited to the supplier ? Ensure verification of evidence of permanent corrective actions and zero defects at both supplier and in plant before closing out GM LAAM Group liaison ? Ensure the preparation and submission of monthly supplier quality performance data to LAAM ? Provide information / feedback on supplier quality performance issues as required ? Participate in GM LAAM WWP supplier quality conferences and meetings as required
Education
Master of Business Administration (MBA)
Nelson Mandela Metropolitan University2009 to 2014
Bachelor of Business Administration (BBA)
Nelson Mandela Metropolitan University2006 to 2008
City and Guilds of London
Nelson Mandela Metropolitan University2005 to 2005
Electrical Engineering
Cape Peninsula University of Technology1998 to 2001
Grade 12
Amazizi High School1993 to 1997
Languages
IT skills
Other Skills
More Putuma
Career Goals
Industries of interest
Areas of interest
Availability to travel and work outside the city
No